Compact nanocrystalline soft magnets using Field-Assisted Sintering
Motivation
This transfer project is based on a successfully completed DFG project (SPP1959: BR 1844/21-1/2), which studied the simulation of temperature distribution and grain growth during field-assisted sintering technology (FAST/SPS). The know-how obtained in the completed project will be transferred to an industrial application in the applied project. This project will start at technology readiness level (TRL) 4. The developed numerical model will be the fundamental basis for further developments in the application-oriented field of manufacturing compact nanocrystalline soft magnets.
In this transfer project, FAST/SPS will be used for the processing of compact nanocrystalline soft magnets (Finemet Fe73.5Cu1Nb3Si15.5B7 (at.%)) in order to produce soft magnetic components with geometric diversity, high power density, and low hysteresis and eddy current losses. The compact design makes the typical plastic housing of the commercial wounded cores unnecessary which allows the operation of the components at up to 300°C, instead of 150°C. These improvements are currently of extraordinary interest for the miniaturization and the efficient energy conversion in the field of soft magnets. The compacted materials should be able to be manufactured into different inductive components depending on their magnetic permeabilities, so that a wide range of applications is possible. Preliminary investigations showed that the processing of amorphous flakes made from melt spun ribbons could help to achieve promising properties of the products, as the soft magnetic properties can be directly adjusted by selecting suitable flake sizes for manufacturing. However, the flakes with different size distributions could lead to completely different temperature distributions in the compaction process, which results in inhomogeneous microstructures. Therefore, to assure a homogenous temperature distribution within the required temperature window, the numerical simulation is necessary.
Project contents
The gained knowledge and the developed methods from the completed DFG project provide a solid basis for the processing of compact nanocrystalline soft magnetic components and the industrial application in this transfer project. With the further developed models, the conceptual ideas for the homogenization of the temperature distribution and the compaction of soft magnetic material during FAST/SPS will be tested in virtual, iterative simulation loops, and subsequently applied in the manufacture of the demonstrator. In this way, the currently well-employed trial and error methodology can be replaced by a straightforward procedure which saves time, recourses and cost.
- Further development of the numerical simulations for a precise prediction of the temperature distribution in the powder compact of the soft magnetic material during FAST/SPS process.
- Further development of the material-specific numerical model for the simulation of the compaction of the soft magnetic material during FAST/SPS with the consideration of the temperature distribution in the powder compact.
- Understanding the densification mechanisms of amorphous powders with low electrical and thermal conductivity in the FAST/SPS process.
- Demonstration of the manufacturing of ring-shaped component with homogeneous microstructure from amorphous flakes with poor electrical and thermal conductivity by FAST/SPS.
- Realization of homogeneous temperature for lagre complex-shaped components with the methods of selective electrical insulation and modification of tool design.
- Implementation of the technologies of modeling and simulation in the process development and production of the demonstrator with a upscaled and complex-shaped geometry.
- Saving of resources (time, energy, material), since the implementation and application of the PID controller in the FEM simulation requires less trial-and-error tests.
Project partner
- Fraunhofer IFAM, Dresden
- Magnetec GmbH
Funding
Funded by German Research Society
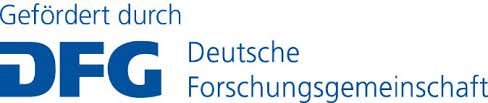