Development of Binder Jetting for highly stressed drive components by sintering according to requirements
Motivation
Powder metallurgical (PM) gears are porous and not as gears made from fully dense, melt-metallurgical material. The densification rolling process can increase the edge density up to 100% thereby strengthen the surface of PM gears, therefore in this way the load bearing capacity of the conventional 16MnCr5 gear steel can be thus matched or even exceeded. Porosity in the component core is accompanied by a reduction in weight and potential optimization of the operating behaviour ("Noise Vibration Harshness"). Due to the applied special powder metallurgical production of gears using powder die compaction and sintering is only economical in large series production. Compared to this conventional production route, Binder Jetting (BJT) is a multi-stage, generative manufacturing process, which is mainly used for flexible prototype production. It can provide an economical solution to the conflicting demands of near-net-shape (NNS) production of gears in small batches. During a BJT process, the green body is produced in layers by the selective deposition of binding material into the powder bed. In the subsequent debinding and sintering processes, the green body is converted to consolidated component. Final geometry, porosity and strength of BJT produced components are achieved after sintering. Therefore, material flexibility in BJT is only limited by the sinterability of the powder. Additionally, the anisotropy of sintering shrinkage is caused by the layered structure of the component in building direction. Therefore, NNS production is only possible by balancing printing and sintering parameters. In comparison to the conventional economical production of high-performance gears of identical geometry in larger quantities, the development of the BJT process for the case-hardening steel powder 16MnCr5 is necessary, which is not suitable for conventional die compaction. Fundamental investigations of both the powder spreading process and the subsequent selective deposition of a liquid binding material are necessary to check the suitability of a material for BJT. The effect of these varying parameters on the sintering process as well as the resulted shrinkage and component profile deviation are to be analysed by manufacturing test samples. Flat bar tension and vibration tests which are used to compare the tensile strength of the green body and the final component after sintering can provide information about the mechanical properties of the tested material. Only when the mechanical properties of the samples are confirmed to be good, the BJT process can be verified for manufacturing a gear prototype that would meet the requirements of the application.
Project contents
In the project, the powder spreading process (modelled by discrete element method) and the sintering (modelled by the finite element method) are numerically simulated across the process chain with the consideration of the powder properties and process parameters. In particular, the further development of the sintering model to consider anisotropic shrinkage with the experimental verification are novel. In this way, the anisotropic sintering shrinkage and the final geometry of a BJT component can be predicted precisely. The case-hardening steel 16MnCr5 and the high-speed steel HS6-5-3 are two materials that are being investigated for the first time in terms of BJT and sintering process. The planned work is listed as follows:
- Characterization of powder and binder materials
- Investigation of physical phenomena during binder jetting
- Simulation and prediction of the local density distribution in the powder bed
- Simulation of anisotropic sintering shrinkage
- Experimental investigation of green density distribution and sintering distortion
- Mechanical characterization to determine the green strength, tensile strength and fatigue strength of the sintered BJT component.
The results will be used to understand the influences of powder properties on the anisotropic sintering shrinkage as well as the influence of binder properties on the BJT process. The simulation method and developed numerical tools will be applied to predict the relative density in the powder bed after powder spreading process and subsequently in the sintering simulation to predict the shrinkage and distortion. Studies based on fatigue tests on specimens produced by both powder die compaction and BJT will allow the comparison of the two processes to check the potential of BJT fabrication for the cyclically highly stressed components.
Project partners
WZL at RWTH Aachen University
Funding
Funded by German Research Society
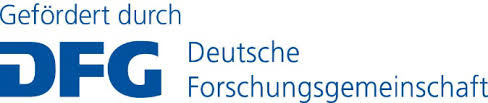