Simulation of the machining of Inconel 718
Experimental and model-based analysis of machining-induced residual stresses and component distortion during turning of Inconel 718
Motivation
The functionality, operational behavior and service life of highly stressed, safety-relevant aircraft engine components made of the nickel-based alloy Inconel 718, are largely determined by the manufacturing accuracy and the edge zone properties. Therefore, high demands are placed on finished turbine parts with regard to geometrical deviations as well as residual stresses and changes in the material microstructure in the edge zone. The adjustment of these component properties is usually determined by the final machining of forged and subsequently heat-treated semi-finished products. During machining and particularly in turning operations, due to the existing thermo-mechanical load collective, residual stresses are introduced near the edge zone, which are superimposed on the inherent residual stresses resulting in component distortion that is difficult to control. An accurate prediction of residual stresses and machining-related component distortion could be achieved by a cross-scale numerical modeling approach which leads to prevention of time-consuming and cost-intensive post-treatment or component rejection.
Objectives
- Determination and modeling of the thermomechanical load during the machining of workpieces made of the alloy Inconel 718 under varying process parameters
- Characterization and modelling of the constitutive material behavior
- Creation of a uniform FE-based calculation model for predicting distortion during the machining of heat-treated components made of Inconel 718
- The application and validation of the developed models using the machining of a hardened engine turbine ring
Project Contents
- Material characterization, in solution annealed and aged state, in terms of microstructure, thermomechanical properties, and residual stresses.
- Simulation of the heat treatment process and kinetic of precipitation
- Dislocation-based modeling of strengthening mechanism
- Investigating the variation in solution annealing and aging treatment processes using dilatometer measurements and SEM microstructure analysis
- Digital-Image-Correlation (DIC) analysis of the corresponding local strain and strain velocity fields induced in the edge zone
- Implementation of a material model and 3D FE simulation of the longitudinal turning process
Project partner
Laboratory for Machine Tools and Production Engineering (WZL)
Funding
Funded by German Research Society
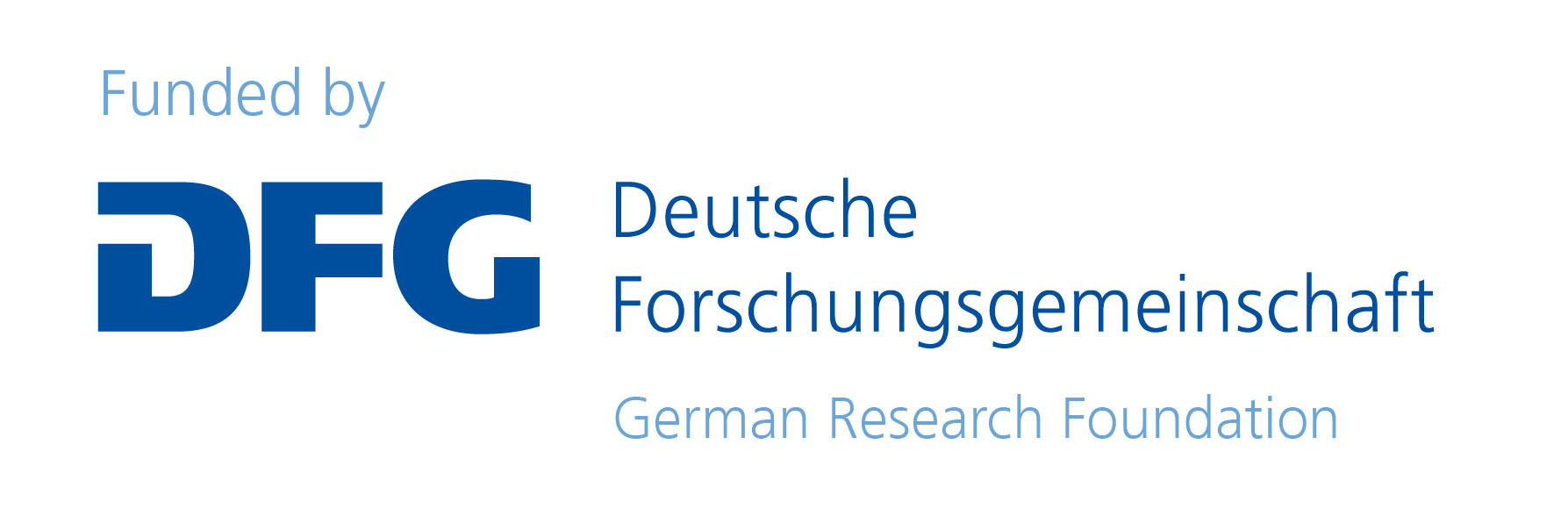